長沙理工大學的FNX-17華曙高科定制版賽車,運用3D打印技術以實現賽車輕量化和優質化
https://www.toutiao.com/i6509234052430561800/
相較于去年的FNX-16,長沙理工大學汽機學院CRT賽車隊的FNX-17延續往年成熟經驗,運用3D打印技術以實現賽車輕量化和優質化。其方向盤、立柱、進氣總成、搖臂等41個關鍵零部件均采用華曙高科先進的3D打印技術,其中60%采用了金屬3D打印技術。賽車各零部件嚴絲合縫,車身設計、結構、輕量化等性能更優異,整備質量僅為225KG,加裝限流閥后最高時速可達140Km/h。
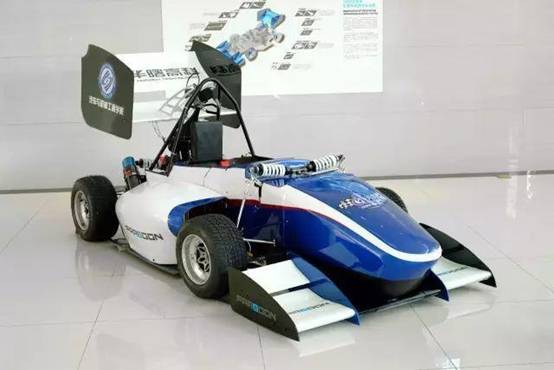
FNX系列賽車,名字源自于“Phoenix”一詞,象征著鳳凰涅槃之意,同時也體現出CRT車隊不斷創新、不斷進取的精神。賽車繼承了車隊設計理念的精華,進行了大量的創新,并運用了湖南華曙高科技有限責任公司多項3D打印設計和制造技術。
從設計到最后完工,他們用了一整年。在FNX-17的設計制造過程中,運用了大量的虛擬仿真分析和優化計算方法,實現了整車輕量化、可靠性提升和整車性能優化。如通過輪轂輪輻一體化設計,3D打印輪轂,使車輪共減重2kg。更多采用相同規格的耳片或安裝接頭,提高了零部件通用性,縮短設計及制造周期。
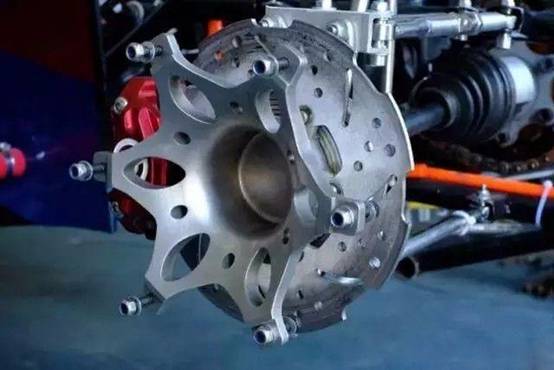
輪輻輪轂一體化的結構能使汽車更好地實現輕量化,若使用傳統減材制造方式,材料去除率高達到93%,浪費嚴重,而金屬3D打印技術能使此類異型零件一體成型,在曲面型零件制造中具有絕對的優勢。
同時賽車的其他性能上也進行了優化,如三球銷外殼的聯軸器結構設計提高了系統可維護性,采用干式潤滑系統提高了賽車高速轉彎時的發動機潤滑性能,采用電子水泵精確控制發動機水溫區間提高了車輛可靠性,運用電動氣動換擋以實現了起步控制和自動升檔,縮短了換擋時間,采用電子節氣門提高了油門響應速度和精度等等。
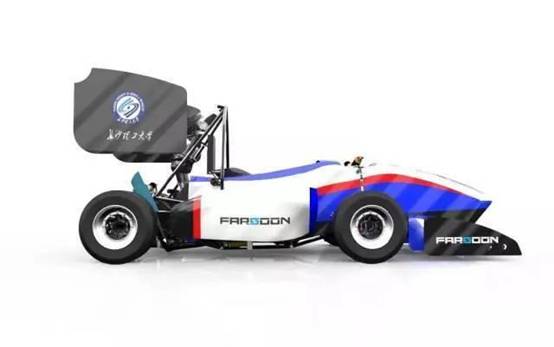
長沙理工大學與湖南華曙高科技有限責任公司自2013年開始合作,連續四年將3D打印技術應用于大學生方程式賽車。FNX-17華曙高科定制版賽車,則是今年車隊與其共同研制的一款賽車,并將作為華曙高科3D打印技術在汽車行業的應用示范。
賽車上數十個形狀和結構復雜、傳統工藝加工困難的零部件,CRT車隊開展了3D打印設計和制造。如排氣系統二合一接口、進氣系統穩壓腔和進氣歧管、懸架系統立柱、轉向系統支撐結構及方向盤、大部分的空氣動力學套件等。3D打印賽車零部件經過華曙高科工程師和長沙理工CRT賽車隊合作優化設計,兼顧了輕量化和強度的雙重要求,對賽車燃油經濟性和安全性等性能的提升具有重要意義。
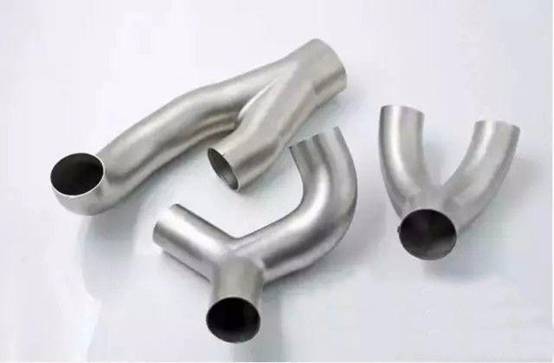
采用金屬3D打印的排氣第二歧管包括其二合一接頭部分,一方面避免了傳統焊接工藝帶來的密封性不佳等問題,使歧管內壁更加光滑氣流通過更加順暢,后期焊接難度也大大降低;另一方面不受實際加工水平限制,歧管形狀可完全根據仿真分析優化后的數據制造,使設計意圖得到最佳體現。
賽車上有41個零件是采用的3D打印技術,未來將有更多的汽車零部件可以采用3D打印技術。3D打印不僅是制造技術,更為設計師的設計開拓了一片嶄新天地。以賽車發動機進氣系統為例,新的3D打印賽車進氣系統進行了一系列仿真優化,在保證一定進氣系統流動均勻性的基礎上,提高了發動機的充氣系數,基于3D打印技術制作的進氣歧管可以使設計者發揮出進氣系統的最大潛力,而不需受制于傳統加工工藝。
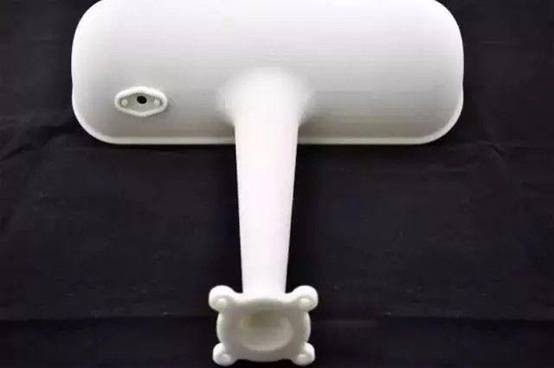
采用尼龍3D打印技術打印進氣腔,有效避免傳統加工工藝局限,能滿足賽車輕量化,高強度等要求。
3D打印技術的產業化發展迅速,特別是在汽車、航空航天等領域,方程式賽車是典型的汽車應用,可充分地發揮金屬、尼龍3D打印的獨特優勢。